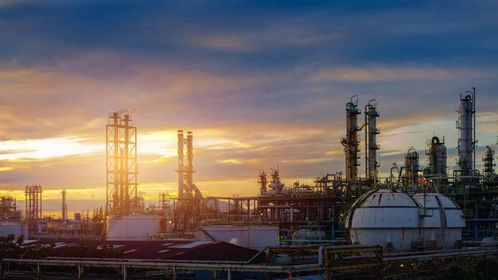
1技術來源
東華工程科技股份有限公司自主研發“煤化工廢水零排放技術”,可以實現煤化工廢水全部資源化利用,無任何液態廢物外排,同時對濃鹽水分鹽結晶。
2基本原理
該技術包括污水處理、污水回用、反滲透濃水膜濃縮、濃鹽水蒸發結晶等系統。
污水處理具體的工藝路線為:預處理+多級生化+深度處理。
回用水系統秉承分質處理、分質回用的原則,關鍵工藝路線為:軟化澄清+過濾+超濾+反滲透。
反滲透濃水膜濃縮工藝路線為:軟化澄清+過濾+離子交換+納濾+深度濃縮。
濃鹽水蒸發結晶工藝路線為:多效蒸發濃縮+強制循環分段結晶。
3工藝過程
本廢水零排放技術包括污水處理、污水回用、反滲透濃水膜濃縮、濃鹽水蒸發結晶等技術。
污水處理具體的工藝路線為:調節+隔油沉淀+混凝氣浮+水解酸化(厭氧)+一級生化+二級生化+混凝沉淀+高級氧化+深度生物處理+過濾吸附。
污水回用根據來水水質的不同設置生化污水回用和含鹽廢水回用兩個系統,回用工藝路線為:軟化澄清+過濾+超濾+反滲透。
蒸發結晶分鹽工藝采用納濾+熱法分鹽的組合,結晶母液采用熱風干化蒸發工藝。
4技術特點
①本技術將煤炭加工、轉化過程中產生的所有廢水收集處理后回用,無任何廢水外排,既保護了自然環境、防止了污染、又節約了新鮮水資源。回用水處理程度高,回用水水質好,優于《工業循環冷卻水處理設計規范》中的再生水水質指標,與新鮮水水質相當,可回用于部分生產裝置的工藝用水。
②采用適合煤化工廢水處理的多級生化反應系統。為避免生物毒性抑制,首先采用厭氧水解酸化工藝對含酚廢水進行預處理,既提高了污水的可生化性,又避免了多元酚向醌類物質的轉化。生化段采用“全混式鼓風曝氣氧化溝+推流式A/O”的兩級生化處理工藝,兩級生化的CODcr總去除率達到90%以上。從而攻克煤化工綜合廢水有機物濃度高、難生化及生物毒性強的水處理難題。
③深度處理段采用化學、生物、物理聯合技術,出水水質好,CODcr≤60mg/L,NH3-N≤5mg/L;“化學藥劑+高級氧化+深度生物處理”技術的使用,對生化出水有機物進行深度去除;兩級活性焦工藝做為保安措施,可靈活應對煤化工廢水的水質波動,確保出水穩定達標,兩級可前后置變換調節的設置,提高了吸附能力及運營管理的靈活性。
④蒸發結晶段采用“納濾+均相膜電滲析”的耦合工藝,實現煤化工廢水的分鹽及深度濃縮。
5技術水平
該技術已獲得石油和化工行業環境保護與清潔生產重點支撐(設備)技術,依托于該技術建設的伊犁新天年產20億立方煤制天然氣項目被評為國家優質工程金獎、全國化學工業優質工程、綠色建造設計水平評價一等成果獎、及安徽省優秀勘察設計一等獎。該技術解決了煤化工廢水資源化利用的難題,為我國煤化工污水零排放領域提供了創新的組合工藝,技術水平達到國內領先。
6節能減排狀況
(1)本技術將廢水處理后全部回用,使廢水資源化,不向自然環境排放任何廢水。可消減污染物排放量如下:
廢水量:1599.12萬m3/a;
CODcr:27442.8 t/a;
NH3-N:1764.18 t/a;
危險廢物:25600 t/a。
(2)所有廢水經處理后全部回用,節約新鮮水1599.12萬m3/a。
(3)多級反滲透濃縮,將多效蒸發的規模縮小一倍,大大節約蒸汽用量和循環水量。每年可節約蒸汽約94萬噸,節約循環水量約3000萬噸。
(4)采用多效蒸發(四效)裝置,比單效蒸發大大節省蒸汽用量和循環水用量。節約蒸汽約220 t/h,節約循環水量約12990 t/h。
(5)低壓蒸汽冷凝液回收利用,回收量約120 t/h。
7技術應用條件
本技術可應用于煤化工行業廢水處理、中水回用、蒸發結晶等領域。
8應用實例與效益
本技術已應用于伊犁新天年產20億立方煤制天然氣項目污水處理及回用工程中。實現廢水全部資源化利用的同時,將濃鹽水中的鹽分級結晶,得到工業級純度結晶鹽,變廢為寶,節約了新鮮水用量,減少危險廢物產量,具有顯著的經濟效益和環境效益。
(來源:中國石油和化工勘察設計協會) |